Safety First
At Texas Controls, we have SAFETY embedded in our culture. Our strong belief that there is always room for improvement, lead us to establish, years ago, our internal Safety Committee. This committee is formed by engineers from our Tech Center, by safety technicians as well as field supervisors with extensive experience as users.
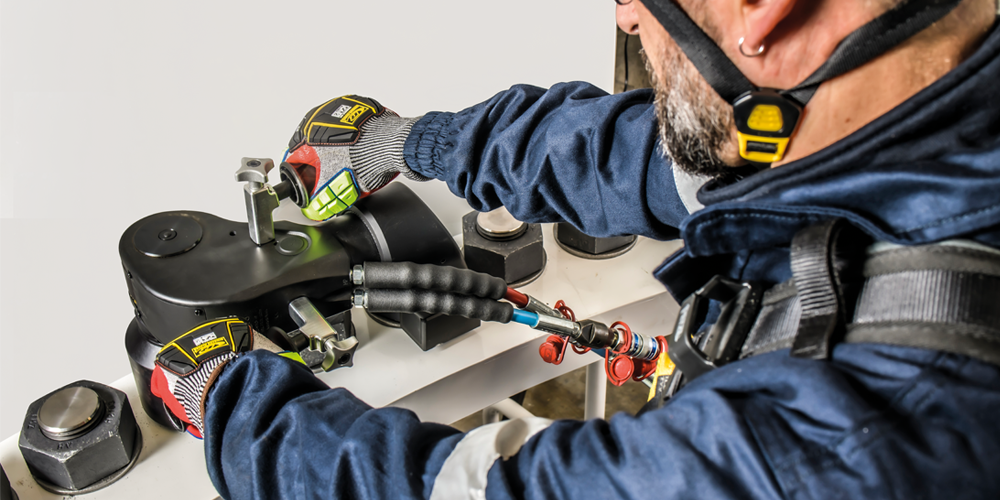
Our Differentiated
Safety Solutions:
Safe reaction points
The extreme levels of forces and pressures generated during bolt tightening activities have to be taken seriously, from a Quality but also from a Safety perspective. Safety is everybody’s responsibility, therefore a corporate one and will only be achieved through the right leadership.
Every single design or development is analyzed and filtered by this committee before validation, but also existing tools and systems through constant collaboration with real users. Understanding the job to be done, deep risk analysis, hazard identification and Real Root Cause Analysis (RRCA) of past incidents enrich our potential to come out with the safest solutions.
Tool Design:
As much as possible, the design of the tool needs to limit the possibility of hands and fingers being placed in potential pinch points when instinctive or reflex uncontrolled action. Our tools are designed with this objective and in our automated systems, pinch point access is almost impossible.
More informationSafety handles
Our easy to position and weight balanced double safety handles were born to meet several purposes: Operator Comfort, ergonomic handling and avoiding hands and fingers being placed in potential pinch points.
More information
Safe pressure pumps
Our pumps are designed in a way that when stopped
(even through emergency stop), all pressure
is released.
Operator Control
Higher torque values require heavier tools and therefore two operators. Any miscommunication between the tool operator and the pump operator can lead to an incident. We designed the best Enabling and Safety Switch, with which the tool
operator is in total control not depending on the pump operator.
Tool Operation
Double ratchet tools, as well as some electric tools, maintain reaction force when pressures it’s released or even in retract mode. In most occasions, double ratchet tools need pressure increase to liberate the second ratchet; just imagine the extra suffering and damage that this means. We design our torque tools in a way that as soon as advance pressure is not activated, reaction is eliminated.
More informationSafe Reaction Arms
The designs of our reaction arms are not only easy to position but are run through a safety filter, limiting hand and finger entrapment by uncontrolled reflex actions. Also, continuous designs of application specific reaction arms are part of our daily activities.
OTHER SAFETY SOLUTIONS: OIL PROJECTIONS
The extreme levels of hydraulic oil pressure and the consequences of such oil coming into our body, should make us all aware of this potential hazard.
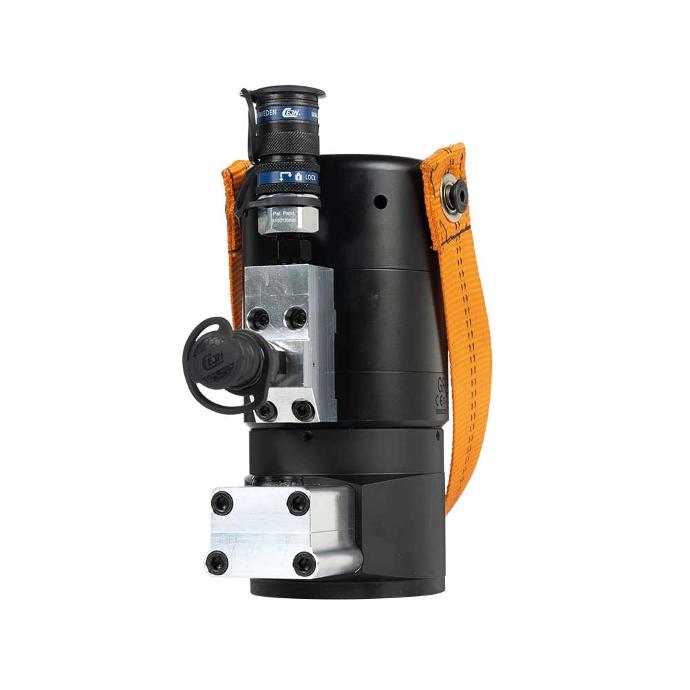
Tensioners
Our tensioners are designed to redirect any oil leak to the bolt avoiding a radial projection
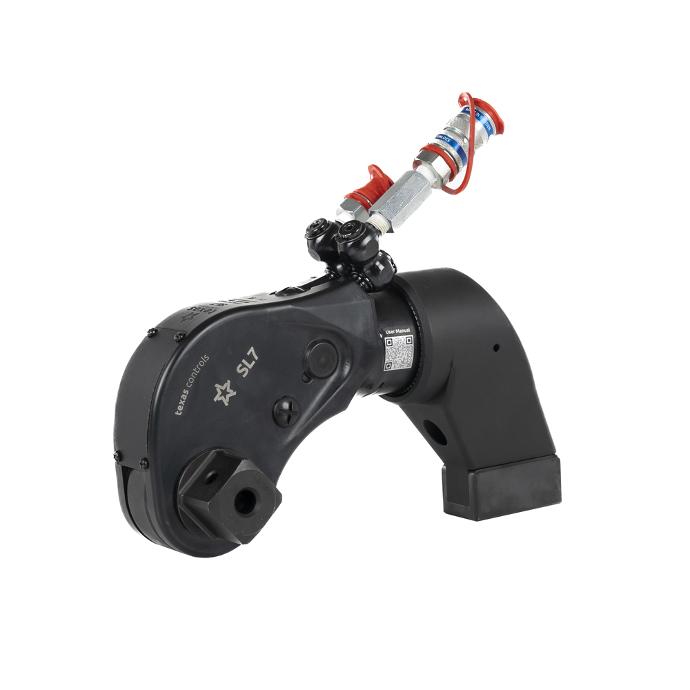
Hydraulic wrenches
Our wrenches are designed with the highest mechanical integrity security ratios in our industry.
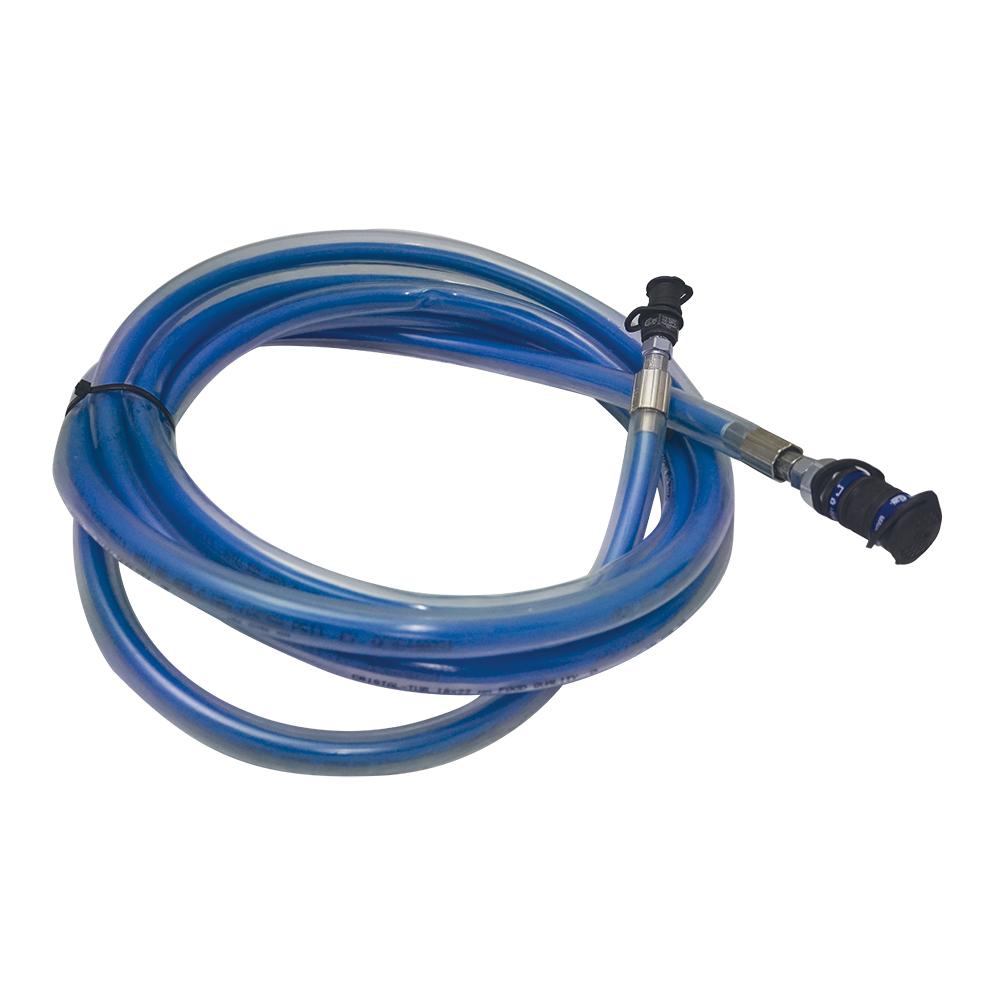
Our hoses
We only use hoses and connectors above the tool pressures and with safety shields.

Our pumps
Supply pressure up to 2000 bar. Designed so that the elements interacting with the operator are opposite the high pressure points.
ENSURING THE SAFETY
IN WORKING ENVIRONMENTS
Addressing Electrical Challenges, Mechanical Hazards and Accident Prevention during Tool Handling and Lifting
LIFTING AND HANDLING
pump safely in its frame since most of the pumps in the market are only supported by 4 small bolts to the frame, breaking quite easily and falling out of the framewhile lifting our handling.
• Certified lifting points to 2.5 times the pumps weight.
• Minimum 8 fixing points motor to frame working at shear and tension.
Electrical issues
Surprisingly, most power packs in the industry do not have circuit breakers. Electrically systems of this type, being powered by generators in many instances, continuously moving from power cords and plugs in a field environment, should always have over-current /over-voltage protection. For us this is a must:
• Thermal Circuit Breakers
• Emergency Stop Switch
• Heavy Duty Shielded Cables
Mechanical projections
A tensioner’s puller failure while strongly pressurized can become a dangerous cannon ball, and this is something to really take into account in an industry where is not possible to force operators to not stand in the tensioner / bolt axis. The extreme levels of forces and pressures can force a tensioner, torque wrench, manifolds... to explode, to blow out. The wrong impact socket, especially in an industry that space restrictions forces reduced walls in such items, can be a hazard point. We take these aspects very seriously:
• Closed Wind Turbine Tensioner Designs have been tested and certified by an independent certification entity to prove that puller failure will not allow the tool to move, jump or fly away from the bolt.
• All our tool designs require a minimum mechanical integrity safety of at least 1.6 being 2.0 + the average.
• Any new design runs full pressure testing of at least 10,000 cycles, witnessed and certified
by independent certification companies.
• Safe and robust impact sockets with the right fixing system square drive to socket.
• Finite Element Analysis for optimal impact socket custom designs and ductile materials to avoid metal chips projections.
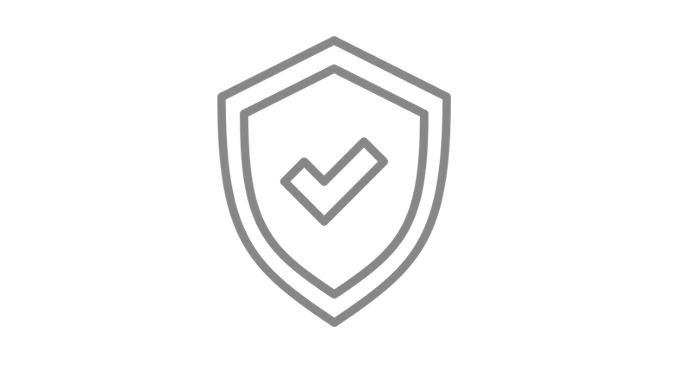
Contact Texas Controls
Get in touch with us